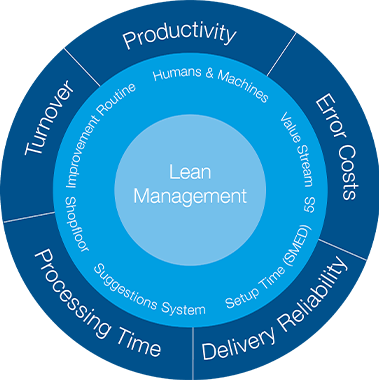
KANBAN was followed by lean management: It encompassed all areas of operation and minimised any unproductive waste of time, energy, labour and materials.
From the mid-1990s, Franke made significant changes to its production processes. The success of CT bearings and aluminium roller guides required new approaches in terms of manufacturing quality and production organisation. The same applied to new low-cost variants for bearing elements and bearing assemblies, which were increasingly being produced in series in larger quantities.
The innovations began in 1995 with the introduction of standards and quality management in accordance with DIN ISO 9001. The certification was accompanied by big investments in the development of new machines for the automated, consistently high-quality grinding of races, which had previously been mainly dependent on the experience and expertise of employees. In 1996, the Positioning Technology division was separated from the Bearing and Linear Bearings division and organised into an independent product group. The principle of self-organising production units was being transferred to all product areas – primarily in order to be able to react more flexibly, quickly and efficiently to changing order volumes.
To make optimum use of the advantages of group work, Franke introduced an organisational principle in 1998 that had caused a furore in Japanese automobile production: KANBAN. This method of controlling production processes ensured that materials and preliminary products were always at the production site in the right quantities when they were needed. Extensive – and expensive – stockpiling was no longer necessary. In contrast to the previous centralised production control system, the teams could – and had to – organise the provision of required preliminary products flexibly and independently. Regular meetings on production and logistics planning therefore became part of the group work.
KANBAN was later developed further and integrated into the principle of lean management. This offers a comprehensive “toolbox” containing a variety of harmonised methods and processes designed to avoid waste of all kinds. Today, Franke’s lean management has numerous carefully established control systems that ensure flexible, efficient use of resources and consistently high production quality for both series and individual production. //